Minchen Gears: Revolutionizing the Automotive Industry with Advanced Gear Solutions
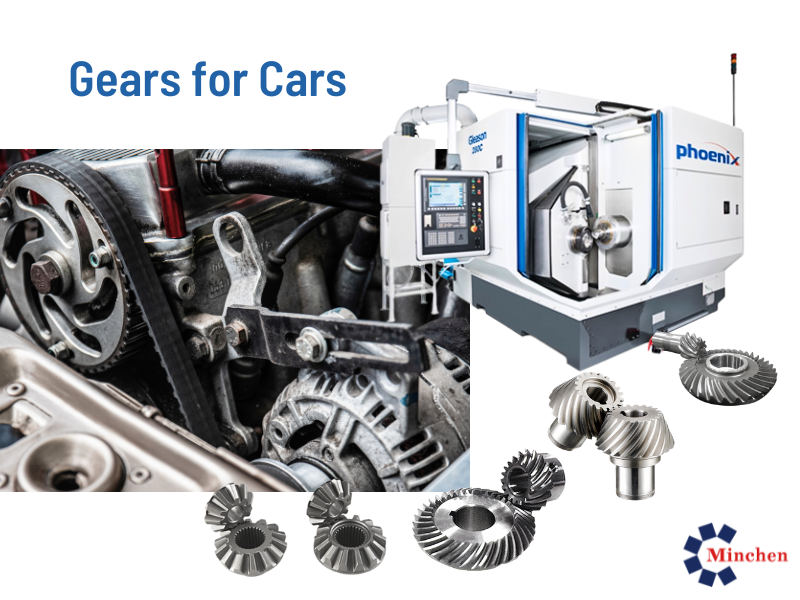
Introduction:
Since its inception in 1968, Minchen Gear has stood at the forefront of bevel gear manufacturing in Taiwan. With an unyielding commitment to quality and innovation, Minchen has evolved into a specialized developer and manufacturer, particularly in the automotive sector. This article delves into the intricate world of vehicle gears, showcasing Minchen's advanced products and the cutting-edge technology behind them.
1. GRINDING GRADE SPIRAL BEVEL GEAR for Vehicles:
A critical component in the differential of a vehicle, the grinding grade spiral bevel gear plays a pivotal role in transmitting power to the wheels while allowing them to rotate at different speeds. Minchen utilizes state-of-the-art GLEASON PHOENIX® 280C and GLEASON PHOENIX®II 275HC CNC cutting machines, ensuring precision and durability. These gears are integral to enhancing the vehicle's handling and performance, particularly in high-speed or off-road conditions.
2. FORGING, HYPOID GEAR for Vehicles:
Hypoid gears, known for their offset gear axes, are essential in modern vehicles for smoother and quieter operation, especially in rear-wheel drives. Minchen's expertise shines in its use of the KLINGELNBERG C27 for precision cutting. The hypoid gears are designed to offer superior contact strength and longevity, contributing significantly to the differential's efficiency.
3. FORGING, STRAIGHT BEVEL GEAR for Vehicles:
Straight bevel gears, though simpler in design than spiral or hypoid gears, are crucial in various vehicle applications like differential systems. Minchen’s manufacturing process, involving advanced CNC machines, ensures these gears meet the highest standards of accuracy and strength, making them suitable for a range of vehicles.
4. FORGING GEAR for Vehicles:
The forging process used by Minchen imparts superior mechanical properties to gears, making them ideal for high-stress applications in vehicles. The FEELER VMP-40A and KITAMURA VERTICAL MACHINING CENTER VMX-1300 play a vital role in shaping these gears, ensuring they can withstand extreme conditions while offering optimal performance.
Technology at Minchen:
Minchen’s manufacturing prowess is backed by an array of GLEASON and KLINGELNBERG machines. The CNC Lapping Machine GLEASON 600HTL enhances the smoothness and accuracy of gear surfaces, while the KLINGELNBERG SPIRAL BEVEL GEAR GRINDING MACHINE G30 ensures the highest precision in gear grinding. These technological advancements allow Minchen to produce gears that are not only durable but also incredibly efficient.
Spotlight on Key Machines:
GLEASON PHOENIX® 280C CNC Cutting Machine:
- Specialty: This machine is renowned for its advanced technology in cutting spiral bevel gears.
- Key Features: It offers high precision and flexibility in gear cutting, which is crucial for producing complex gear geometries. The PHOENIX® 280C is especially adept at handling a wide range of sizes and types of bevel gears, making it a versatile tool in the gear manufacturing process.
- Industry Impact: Its ability to produce high-quality gears with tight tolerances makes it a valuable asset in industries where gear performance is critical, such as in automotive and aerospace applications.
KLINGELNBERG SPIRAL BEVEL GEAR GRINDING MACHINE G30:
- Specialty: This machine is specifically designed for the grinding of spiral bevel gears, a crucial step in achieving the smooth, quiet operation of these gears in vehicles.
- Key Features: It excels in precision grinding, ensuring that the gears have an optimal surface finish and accurate tooth geometry. This results in gears with improved load capacity and reduced noise and vibration.
- Industry Impact: The G30's high precision and reliability make it an essential tool for producing high-quality bevel gears used in various automotive applications, particularly for luxury and high-performance vehicles where gear noise and performance are of utmost importance.
These two machines, the GLEASON PHOENIX® 280C and the KLINGELNBERG SPIRAL BEVEL GEAR GRINDING MACHINE G30, represent the cutting edge of gear manufacturing technology. Their presence in a manufacturing setup like Minchen's speaks volumes about the company's commitment to quality and precision in gear production.
Conclusion:
Minchen's commitment to quality and innovation is evident in every gear produced. Catering to the diverse needs of vehicle manufacturers, Minchen's gears are designed to enhance vehicle performance, ensuring smooth operation and longevity. With a deep understanding of the automotive industry's evolving demands, Minchen continues to lead the way in gear manufacturing, solidifying its position as a trusted partner in the global automotive sector.