5 Key Advantages of Forged Gears in Heavy-Duty Applications
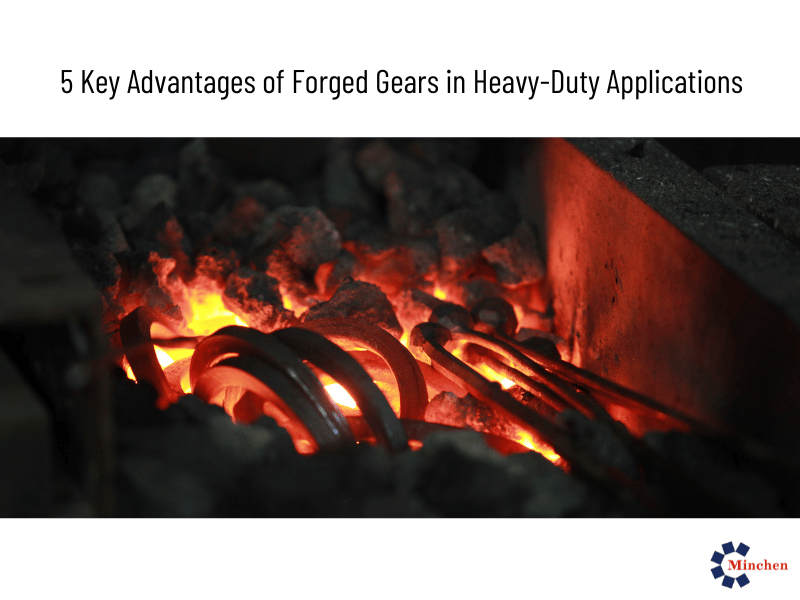
Introduction
In our previous article, "Comparing Gear Manufacturing Methods: Forging vs. Casting", we discussed the fundamental differences between forged and cast gears. While both methods have their place in gear manufacturing, forging is the preferred choice for high-performance, heavy-duty applications due to its superior strength, durability, and load-bearing capacity.
For industries where reliability is non-negotiable—such as construction equipment, industrial machinery, automotive drivetrains, and agricultural machinery—forged gears provide a longer service life and enhanced performance under extreme conditions. Let’s explore the five key advantages of forged gears in heavy-duty applications and why they outperform other gear types.
________________________________________
1. Superior Strength and Load Capacity
Forged gears exhibit exceptional mechanical strength, thanks to the forging process, which refines the metal’s grain structure and eliminates internal voids or defects. Unlike cast gears, which may contain porosity or weak points, forged gears maintain consistent material integrity, allowing them to withstand:
- Heavy loads without deformation
- High torque transmission in industrial machinery
- Extreme pressure in construction and mining equipment
Example: In off-road heavy-duty vehicles, forged gears are essential in differentials and transfer cases, where they endure continuous stress without failure.
________________________________________
2. Exceptional Wear and Fatigue Resistance
Heavy-duty applications expose gears to intense friction, repeated stress cycles, and harsh environments. Forged gears have a higher resistance to wear, fatigue, and impact compared to cast or machined gears, thanks to:
- Stronger grain alignment from the forging process
- Heat treatment capabilities that enhance surface hardness
- Better shock absorption, reducing the risk of sudden gear failure
Example: Industrial reducers used in steel mills or conveyor systems rely on forged gears to ensure long-term operation with minimal maintenance, despite continuous exposure to high loads.
________________________________________
3. Precision and Dimensional Accuracy
Modern forging techniques, combined with CNC machining and grinding processes, allow manufacturers to achieve high dimensional accuracy and tight tolerances in forged gears. This ensures:
- Consistent gear meshing, reducing vibration and noise
- Efficient power transmission, improving energy savings
- Minimized backlash, essential for high-performance machinery
Example: High-ratio hypoid gears in commercial trucks require precise tooth alignment for smooth and efficient torque transfer while handling heavy payloads.
________________________________________
4. Improved Heat Dissipation and Thermal Stability
Heavy-duty machinery often operates under high-temperature conditions, where excessive heat can weaken gear materials. Forged gears have:
- Higher thermal resistance, preventing material degradation
- Better heat dissipation, reducing friction-related wear
- Greater structural stability, even in prolonged high-temperature environments
Example: In wind turbines, forged gears play a crucial role in gearboxes that must operate efficiently for years, despite constant heat and friction.
________________________________________
5. Longer Service Life and Cost Efficiency
While forged gears may have a higher initial manufacturing cost than cast or standard machined gears, they provide greater long-term value by:
- Reducing downtime due to fewer failures
- Lowering maintenance costs, as they require fewer replacements
- Enhancing overall system reliability, improving productivity
Example: Agricultural machinery, such as tractors and harvesters, require highly durable gears that can last for years under heavy workloads, making forged gears a cost-effective investment.
________________________________________
Why Minchen Gear Co., Ltd. for Forged Gears?
At Minchen Gear Co., Ltd., we specialize in manufacturing high-precision forged gears for heavy-duty applications. Our products, including spiral bevel gears, straight bevel gears, hypoid gears, and high-ratio hypoid (HRH) gears, are designed to meet the most rigorous industry standards.
- Advanced forging technology for superior material strength
- Precision CNC machining & grinding for optimal gear performance
- Customized solutions for industrial, automotive, and agricultural applications
Whether you need high-performance gears for industrial machinery, commercial vehicles, or construction equipment, Minchen Gear Co., Ltd. provides reliable, durable, and high-efficiency forged gears to keep your operations running smoothly.
________________________________________
Conclusion
Forged gears are the best choice for heavy-duty applications due to their superior strength, durability, precision, heat resistance, and long-term cost efficiency. Compared to cast gears, forged gears offer better load capacity and reliability, making them essential for industries that demand top-tier performance.
If you're looking for high-quality forged gears for your next project, contact Minchen Gear Co., Ltd. today to learn how our expertise in gear manufacturing can help optimize your machinery's performance.